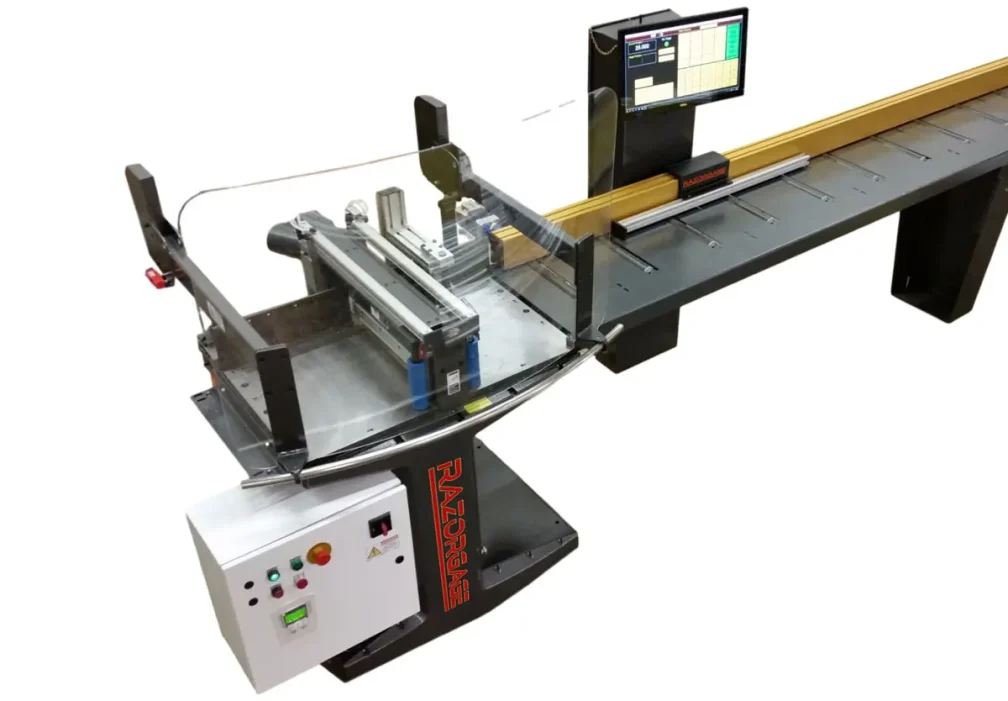
How Can Automatic Saw Systems Improve Manufacturing Efficiency in 2025?
In 2025, precision, speed, and minimal waste aren’t optional; they’re expected. Manufacturing companies in woodworking, window/door fabrication, and aluminum extrusion are under greater pressure to deliver faster lead times, greater consistency, and more customization with less overhead. That’s why automatic saw systems have become an essential upgrade across industries looking to stay competitive.
Manual workflows are simply not built for this new reality. They invite human error, cause delays in cut cycles, and lead to costly material waste. By integrating smart technology like the Automatic Pusher System, RazorOptimal, and RG3 Positioner, manufacturers can unlock measurable gains in productivity and output without sacrificing accuracy.
Let’s explore how the shift to automation is not just about keeping up, but moving ahead.
What Are Automatic Saw Systems?
Automatic saw systems are smart, motorized setups that combine cutting machinery with digital positioning tools to streamline the cutting process. Instead of manually setting stops or measuring each length, these systems do the work for you, backed by software-driven cut lists and high-speed material positioning.
These setups aren’t limited to one machine. A modern automated saw system might include:
- A programmable stop/pusher for length precision
- A digital interface that loads and sorts cut lists.
- A saw station, such as the RazorOptimal, that executes precise cuts without delay.
- Label printing to ensure correct part tracking downstream
Together, these components form a closed-loop cutting system, reducing dependency on skilled labor while improving speed, consistency, and overall efficiency.
What’s Driving the Shift in 2025?
Industry expectations have shifted. Companies are responding to several major changes:
- Increased customization: Shorter product runs and more varied sizes demand flexibility.
- Skilled labor shortages: Entry-level staff need tools that are intuitive and reduce onboarding time.
- Rising material costs: Mistakes are expensive. Each cut needs to be accurate, from start to finish.
- Demand for real-time data: Operations teams want to track throughput and reduce bottlenecks.
Automatic saw systems directly address these needs with digital precision and streamlined workflow integration.
5 Ways Automation Delivers Immediate Gains
1. Faster Throughput, Without Human Error
Manual measurements eat up time and increase the chance of miscuts. With RazorGage’s systems, operators simply load a cut list, and the machine positions the material to exact dimensions. The operator can focus on safety and saw control, while the system handles positioning.
Whether using the Automatic Pusher System or RG3 Positioner, manufacturers can expect cycle times to drop significantly, especially in repeatable workflows.
2. Improved Cut Accuracy
When working with expensive materials like metal or hardwood, accuracy is very important. RazorGage’s positioners are made with zero-clearance pulleys and rotating ball linear bearings, which make sure that the movement is smooth and accurate.
Even under daily industrial workloads, these tools deliver exceptional repeatability that operators can trust.
3. Less Material Waste
A miscut doesn’t just cost material, it delays jobs, adds rework time, and creates inconsistency in production. Automated cut-list execution ensures every cut is correct the first time, reducing waste over hundreds or thousands of parts.
Especially in shops using premium stock, the cost savings here scale quickly. With RazorOptimal, RazorGage’s integrated optimizing saw system, businesses achieve smarter material utilization per board or extrusion.
4. Better Workflow Integration
RazorGage’s systems are Windows-based, which allows easy integration into your existing network. Operators can load cut lists from a shared drive, with no manual input required. It reduces the dependency on paperwork, eliminates versioning errors, and allows production managers to track job completion in real time.
You can even sort and group cut lists using multiple criteria, offering more control in batch operations.
5. Reduced Labor Dependency
Automation isn’t about replacing people; it’s about empowering them. A new operator can be trained in minutes to run a RazorGage system. With intuitive touchscreens and user-friendly software, onboarding is faster, and operators become productive much sooner.
That’s a game-changer in industries where experienced labor is hard to find.
RazorGage Solutions Engineered for Efficiency
RazorGage offers several robust systems designed to meet the cutting challenges of today’s manufacturers.
RazorOptimal Saw System
The RazorOptimal is our top-of-the-line optimizing saw system. It’s ideal for cabinet builders, door and window manufacturers, and any shop that needs high-speed, high-precision cut optimization. Unlike standard saw systems, RazorOptimal incorporates both RazorGage positioning technology and advanced optimization algorithms to ensure the most efficient cutting patterns with minimal waste.
Automatic Pusher System
Built for continuous, high-speed material advancement, the Automatic Pusher System is ideal for pushing long stock into cutting or punching stations. It is a perfect match for high-volume aluminum or composite workflows. Durable, accurate, and fully programmable.
RG3 Positioner
The RG3 Positioner is a shop favorite thanks to its durability, precision, and ease of integration. And it can be used as either a stop or a pusher. It works with almost every cutting or drilling station. It works great for both stand-alone and integrated processes thanks to its touchscreen interface and high-torque drive system.
Built for Industry: Flexible Across Applications
Whether you’re building custom cabinetry or framing aluminum window components, the RazorGage system adapts to your workflow.
- Cabinetry – High-volume repeatable cuts with less operator fatigue and scrap.
- Window & Door Manufacturing – Consistent lengths across mullions and frame parts.
- Aluminum Extrusion Processing – Clean, accurate cuts for frame-ready extrusion segments.
Because each system is modular, RazorGage tools integrate seamlessly into existing stations without requiring massive infrastructure changes.
Discover What Efficiency Looks Like in 2025
Efficiency is no longer just about moving faster; it’s about working smarter. Whether you’re a small shop scaling up or an enterprise-level production floor optimizing throughput, RazorGage delivers a clear return on investment through automation, precision, and ease of use.
Ready to reduce waste, cut faster, and eliminate guesswork? Explore how RazorGage’s automatic pusher system can transform your production line in 2025 and beyond.
Frequently Asked Questions
- Which RazorGage product is best for automated cutting optimization?
The RazorOptimal Saw System is purpose-built for maximizing cutting efficiency while minimizing waste. It combines high-speed sawing with intelligent layout optimization. - Can RazorGage systems integrate into existing machinery?
Yes. Systems like the RG3 Positioner and Auto Pusher can be retrofitted onto most saws or drills without requiring major changes to your setup. - How does the software handle cut list imports?
Cut lists can be imported via a Windows network or external storage. The intuitive interface allows sorting, grouping, and job scheduling with ease. - Where can I view all RazorGage tools?
You can explore the full lineup of automatic saw systems and positioning solutions by visiting the website.