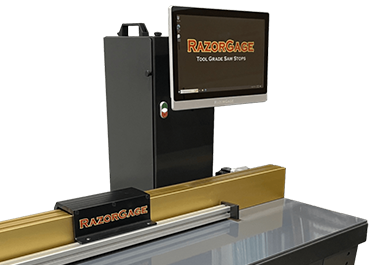
How Do Material Positioning Systems Improve Manufacturing Efficiency?
In fast-paced manufacturing environments, precision isn’t just important—it’s everything. Whether you’re cutting aluminum extrusions or sizing lumber for cabinetry, the speed and accuracy of your cut process directly impacts profitability.
That’s where material positioning systems come into play.
These systems eliminate guesswork, streamline operations, and boost throughput. RazorGage offers high-performance solutions like the RG3 Positioner and APS (Auto Pusher System), built for manufacturers who demand consistency and control across every shift.
Let’s take a closer look at how length stop measuring systems are redefining modern manufacturing.
What Is a Material Positioning System?
A material positioning system is an automated device that moves and precisely positions raw stock before it’s processed, typically cut or drilled. It replaces manual measuring, improves cycle times, and virtually eliminates costly human error.
Instead of a tape measure and a clamp, RazorGage systems use:
- Servo motors for ultra-precise positioning
- linear bearing systems that ensure repeatable movement
- Touchscreen interfaces to enter cut-lists and select jobs.
In short: Less thinking, more doing—with near-zero mistakes.
The Power of Repeatability: ±0.005″ Accuracy
Imagine positioning a piece of stock 10,000 times and hitting the same point every single time. That’s what RazorGage delivers with ±0.005″ repeatability. Whether you’re cutting doors, windows, casework, or structural components, you can trust the cut will be right, again and again.
Why does that matter?
Because miscuts cost you more than material, they create rework, downtime, and frustrated customers. RazorGage systems make those issues vanish.
Not All Automation Is Created Equal
Not all positioning systems deliver the same performance. The difference often comes down to mechanical integrity and software capability, not just motor type. RazorGage systems are built with recirculating ball linear bearings, zero-clearance pulleys, and near-zero backlash gearboxes, ensuring smooth, reliable motion over time.
Paired with Windows-based software, RazorGage offers:
- Fast and accurate positioning
- Smooth motion control with minimal backlash
- Flexible cut-list handling and label printing
- Intuitive operation with advanced sorting features
This combination of robust mechanics and versatile software gives RazorGage a clear edge in demanding production environments.
From Office to Saw: Smarter Cut-List Access Over Your Network
Manual data entry introduces errors, especially when switching between design files and production tools. RazorGage minimizes this risk by enabling cut lists to be transferred digitally over a Windows-based network.
With the APS Optimizing Saw, operators can:
- Access cut lists saved to a shared folder or drive.
- Use a familiar Windows interface to browse, select, and load the right file.
- Avoid repetitive data entry and reduce the likelihood of operator error.
This streamlined process improves job accuracy and keeps workflows connected, without needing to manually rekey cut data at the machine.
Precision Without Complexity
You don’t need a specialist to run RazorGage equipment. The intuitive touchscreen interface allows operators to:
- Manually enter dimensions
- Pull up saved part profiles.
- Adjust on the fly for odd jobs.
Where These Systems Deliver Maximum ROI
Length stop measuring systems and pushers are vital in any shop handling variable-length cuts. Some key industries that see measurable gains:
- Cabinet & furniture makers – Precision fit parts mean tighter joints and fewer returns
- Window & door manufacturers – Complex profiles are cut accurately the first time
- Aluminum & steel fabricators – Bulk runs with near-zero waste
- Glass Industry – Smooth handling of aluminum frames
Anywhere you need speed and exact cuts, a RazorGage system turns a bottleneck into a profit center.
Reduce Material Waste and Rework
Repetitive cuts mean repetitive risk. Even slight inaccuracies can pile up and turn into scrap or rework. But with material positioning systems, you set the cut once, and it’s perfect every time.
Less waste. Fewer miscuts. More profit.
And since RazorGage systems track key performance data and support cut-list processing, manufacturers can monitor output trends, identify bottlenecks, and troubleshoot more efficiently. That level of visibility supports smarter decisions in lean manufacturing environments.
Built for Your Workflow—And Built to Grow
One of the most significant advantages of RazorGage is modularity. Whether you’re upgrading a miter saw station or building a fully automated line, there’s a product to match your needs.
Explore the complete RazorGage Product Line, which includes:
- RG3 Positioner
- Auto Pusher Optimizing Saw System
- Autolist Optimizing Software
Each solution is engineered for plug-and-play integration and future expansion.
Cut Smarter with the Right Tools
Whether you’re upgrading an outdated saw station or scaling a production line, automation shouldn’t be complicated. RazorGage makes it easy to gain precision, reduce waste, and boost throughput with systems that speak your shop’s language.
You’ve already invested in good machines and skilled labor. Now it’s time to invest in the positioning technology that ties it all together.
Ready to make your first move toward leaner, more innovative production? Explore the complete RazorGage Product Line to find the right solution for your operation.
FAQ
- How accurate are RazorGage positioning systems?
RazorGage systems are engineered for ±0.005″ repeatability, making them ideal for manufacturers needing tight tolerances across production runs. - Can I integrate RazorGage systems with my network or ERP?
Yes. Using the AutoList, you can download cut-lists over a Windows network, reducing errors and streamlining job changes. - Which RazorGage system is best for general fabrication work?
The RG3 Positioner is a versatile choice for a wide range of materials and industries, offering both manual and automatic modes with complete servo control. - What if I need a more complete automated cutting system?
For complete automation with push-feed optimization, check out the APS- Auto Pusher System—it combines intelligent cut-list logic with real-time positioning for optimal yield.